Hur man optimerar skruvluftkompressorn
Utgivningstid: 2025-07-15
skruvluftkompressor påverkar direkt produktionskostnader och energiförbrukning. Optimering skruvluftkompressor är inte en enkel parameterjustering, utan ett omfattande projekt som omfattar utrustningsval, systemdesign och driftsledning. Följande delar praktiska optimeringsstrategier från fyra dimensioner.
- Matchande last för att undvika att "en stor häst drar en liten vagn"
Luftkompressorns energiförbrukning är nära relaterad till belastningshastigheten. När den faktiska luftförbrukningen är mycket lägre än den nominella avgasvolymen kommer energiförbrukningen att öka avsevärt. Optimeringspunkterna inkluderar:
Beräkna gasbehovet noggrant: Använd flödesmätare för att övervaka den faktiska gasförbrukningen vid olika tidpunkter, rita gasförbrukningskurvor och välj matchande modeller därefter. För scenarier med intermittent gasförbrukning kan till exempel modeller med frekvensomvandlingsfunktioner väljas för att uppnå automatisk justering av gasvolymen efter behov.
Kontroll av flermaskinskoppling: När gasförbrukningen är stor och fluktuerar ofta används kombinationsläget "1 huvudmaskin + 1-2 hjälpmaskiner", och driften koordineras via den centrala styrenheten för att säkerställa att varje enhet arbetar inom det högeffektiva belastningsområdet (70%-90%).
Kontroll av lossningstidspunkt: Ställ in en rimlig stilleståndstid för lossning (vanligtvis 5–10 minuter) för att undvika att enheten är i lossningsläge under lång tid och förbrukar energi.
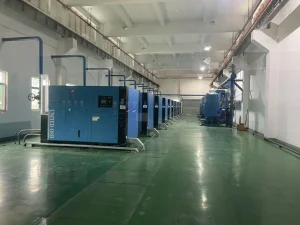
- Optimera gaskretssystemet för att minska tryckförlusten
Tryckförlusten i tryckluften under transport är en osynlig energidödare. Systemoptimering måste fokusera på:
Rationalisering av rörledningsdesign: Huvudrörledningens diameter bör beräknas utifrån den maximala gasförbrukningen för att undvika tryckfall orsakat av för tunn diameter; minska onödiga böjar och ventiler, förkorta rörledningens längd och kontrollera tryckförlusten inom 0,02 MPa.
Matchning av tork- och reningsutrustning: Välj lämpliga torkar (adsorption eller kylning) och filter enligt gaskvalitetskraven för att undvika onödig tryckförlust på grund av överrening. Rengör filterelementet regelbundet för att hålla tryckfallet stabilt.
Läckagedetektering och pluggning: Om läckaget i tryckluftssystemet överstiger 10% kan den årliga energiförlusten uppgå till tiotusentals yuan. Det rekommenderas att använda en ultraljudsdetektor för att kontrollera rörskarvar, ventiler och andra läckagepunkter varje månad och reparera dem i tid.
- Stärk kontrollen av driftsparametrar och förbättra värdens effektivitet
Skruvhuvudenhetens driftstatus avgör direkt hela maskinens prestanda, och följande parametrar måste övervakas:
Inställning av avgastryck: Under förutsättningen att produktionsgastrycket uppfylls kan varje 0,1 MPa minskning av avgastrycket minska energiförbrukningen med cirka 7%. Om till exempel det faktiska gastrycket är 0,6 MPa behöver luftkompressorn inte ställas in på 0,7 MPa.
Kontroll av oljetemperatur och temperaturskillnad: Smörjoljetemperaturen bör hållas vid 80-95 ℃ (oljeinsprutad skruvkompressorFör låg temperatur leder lätt till ofullständig olje-gasseparation, medan för hög temperatur påskyndar oljans åldring. Rengör kylaren och kontrollera temperaturreglerventilen för att säkerställa att temperaturskillnaden mellan inlopps- och utloppsoljetemperaturen inte överstiger 15 ℃.
Övervakning av motordrift: Kontrollera regelbundet motorströmmen och effektfaktorn för att säkerställa att den arbetar inom nominellt område. För högeffektsmotorer kan en variabel frekvensstyrenhet installeras för att uppnå behovsstyrd energiförsörjning.
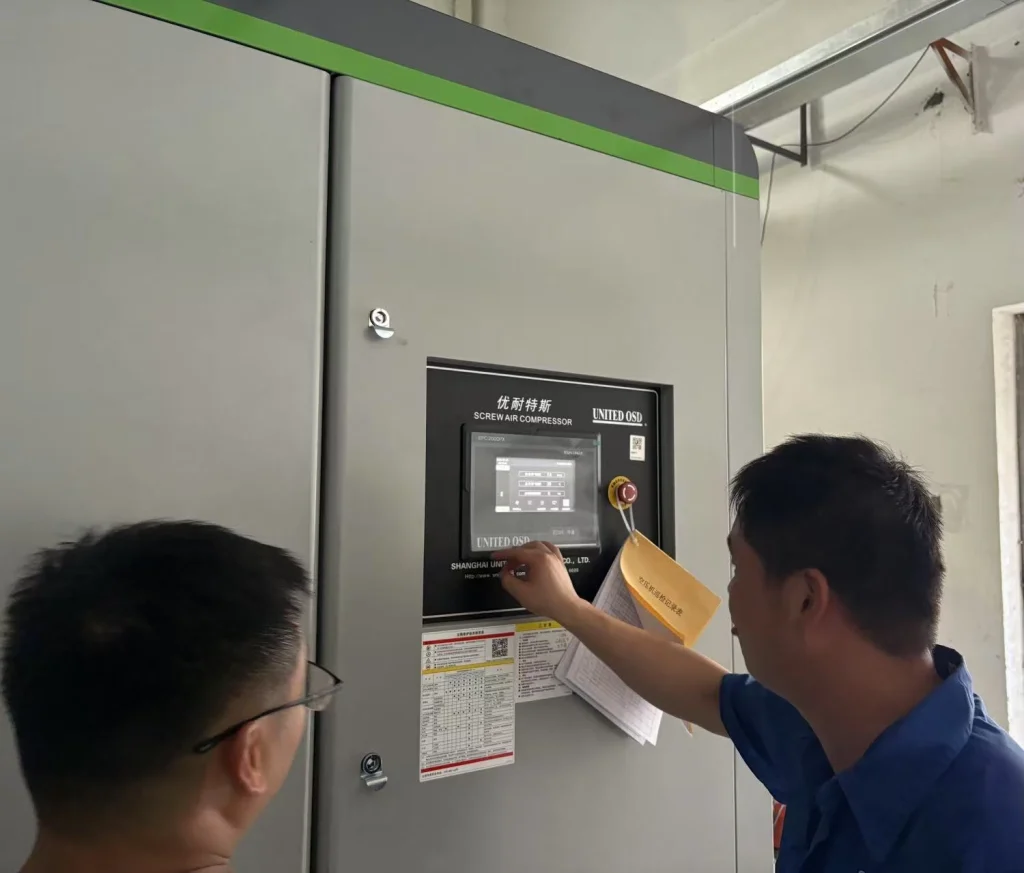
- Vetenskapligt underhåll för att förlänga den effektiva driftscykeln
Utrustningsnedbrytning kommer att leda till ökad energiförbrukning. Systematiskt underhåll är grunden för optimering:
Smörjmedelshantering: Byt specialsmörjmedlet strikt enligt manualen (vanligtvis var 2000-4000:e timme) och undvik att blanda olika oljemärken. Oljenivån måste hållas vid mittlinjen av synglaset och byt ut den omedelbart om oljekvaliteten är onormal (emulgerad, svart).
Inspektion av kärnkomponenter: Kontrollera huvudmotorns rotorspel var 8 000:e drifttimme. Om spelet överstiger standarden måste det repareras i tid, annars minskar avgasvolymen med 5%-10%; rengör olje-gasseparatorns filterelement regelbundet för att hålla tryckskillnaden inom 0,1 MPa.
Optimering av kylsystemet: För luftkylda modeller måste kylaren vara ren och fri från skräp, och omgivningstemperaturen får inte överstiga 40 °C; för vattenkylda modeller måste beläggningen rengöras regelbundet för att säkerställa tillräckligt med kylvatten.
Optimerande skruvluftkompressorer är ett långsiktigt projekt som kräver dynamiska justeringsstrategier baserade på faktisk produktion. Genom kombinationen av "gasförsörjning vid behov, förlustreducering, exakt parameterkontroll och vetenskapligt underhåll" kan energiförbrukningen vanligtvis minskas med 10%-30%, samtidigt som utrustningens livslängd förlängs med 3–5 år, vilket skapar betydande ekonomiska fördelar för företaget. Det rekommenderas att upprätta en driftsbok för utrustningen, regelbundet analysera energiförbrukningsdata och kontinuerligt utforska optimeringsutrymmen.