Air Compressors for Laser Cutting: Enhance Efficiency, Precision & Performance
Release time: 2025-04-14
Laser cutting technology has revolutionized industries such as manufacturing, automotive, aerospace, and even fashion, offering precise, efficient, and fast cutting of a variety of materials. However, the process is highly dependent on specific equipment, including air compressors for laser cutting, which play a crucial role in ensuring smooth operation. In this article, we’ll explore the importance of air compressors in laser cutting, their functions, and how to choose the right compressor for optimal results.
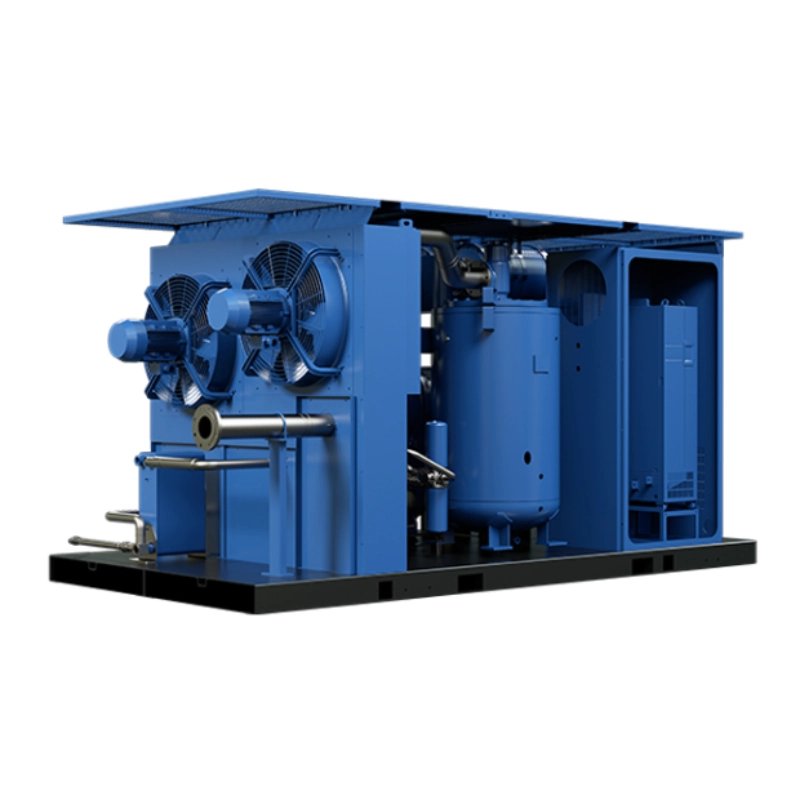
What is Laser Cutting and Why is It Important?
Laser cutting is a process that uses a high-powered laser to cut materials with extreme precision. The laser beam melts, burns, or vaporizes the material along a focused line, leaving behind a clean, sharp cut. Laser cutters are versatile and can cut through a variety of materials, including metals, plastics, wood, and even fabric.
While the laser itself does the cutting, several other components work together to ensure accuracy, speed, and overall performance. One of the most critical components is the air compressor, which provides the necessary airflow to aid in the cutting process.
The Role of Air Compressors in Laser Cutting
Air compressors are essential in laser cutting for several key reasons:
1. Assist in Material Cutting
When a laser cutter cuts through a material, the intense heat generated by the laser can cause debris, slag, or molten material to form around the cut. The laser cutting air compressor blows a high-pressure stream of air at the cutting point, helping to remove these residues and maintain a clean cut. This is particularly important when cutting metals like steel or aluminum, where molten material can easily clog the cut line.
2. Cooling the Laser
Another critical role of the air compressor is to help cool the laser and cutting head. Laser cutting generates a significant amount of heat, and cooling is essential for maintaining the stability of the laser. An air compressor can provide a steady flow of air to cool the cutting area, preventing overheating and ensuring that the laser remains at optimal operating temperatures.
3. Preventing Oxidation
For certain materials, particularly metals, oxygen can lead to oxidation around the cut. This is especially noticeable in materials like stainless steel, where exposure to oxygen can lead to discoloration and rougher cuts. An air compressor for laser cutting helps direct a flow of nitrogen or compressed air to displace oxygen around the cutting area, ensuring a clean, precise cut without the formation of oxide layers.
4. Enhancing Cutting Speed
An air compressor can also enhance the speed of the cutting process. By providing consistent and controlled airflow, the compressor can help the laser maintain its cutting power over extended periods, making the cutting process faster and more efficient. This is especially beneficial when working with thick materials that require more time to cut through.
Types of Air Compressors Used in Laser Cutting
There are various types of air compressors for laser cutting, and the best choice depends on several factors, including the laser cutting machine’s power, the materials being cut, and the required airflow rate.
1. Piston Compressors
Piston compressors, or reciprocating compressors, are commonly used in laser cutting applications. These compressors are reliable, cost-effective, and offer high-pressure output. They are ideal for small to medium-sized laser cutting machines. However, they may not be suitable for high-power laser cutters that require large volumes of air.
2. Rotary Screw Compressors
Rotary screw compressors are often used for high-demand applications due to their ability to provide continuous and consistent airflow. These compressors operate smoothly and have a longer lifespan compared to piston compressors. They are commonly used in larger, industrial-grade laser cutting machines, where reliability and high airflow are essential.
3. Centrifugal Compressors
Centrifugal compressors are designed for very large-scale industrial applications and are capable of delivering high volumes of air at a lower pressure. They are less common for smaller laser cutting machines but are highly effective in high-output environments.
4. Oil-Free Compressors
While traditional air compressors use oil for lubrication, oil-free compressors are designed without oil and are essential when cutting materials like food-grade metals or when air purity is critical. Oil-free compressors provide clean, dry air, which is ideal for applications where contamination can affect the cutting process.
How to Choose the Right Air Compressor for Laser Cutting
Selecting the right air compressor for laser cutting involves considering a few key factors. Here’s what you need to keep in mind:
1. Airflow Requirements
The most crucial factor when selecting an air compressor is the airflow requirement, which is typically measured in cubic feet per minute (CFM). The airflow required will depend on the size and power of the laser cutter, as well as the material thickness being cut.
2. Pressure Requirements
The pressure of the air provided by the compressor is also important. High-pressure systems are typically required for cutting thick or high-density materials like metals. However, too much pressure can cause problems, such as warping or overblowing the material.
3. Energy Efficiency
Energy consumption is another important factor when selecting an air compressor. Choosing an energy-efficient air compressor can help reduce operational costs and ensure that the laser cutting process remains cost-effective over time.
4. Maintenance and Reliability
Choose an air compressor with low maintenance needs and a long lifespan. Consider models with easy-to-replace parts, reliable warranties, and advanced monitoring features that provide real-time diagnostics.
5. Size and Space Considerations
Depending on your workspace, the size and portability of the compressor may be important factors. Larger compressors may be required for high-demand environments, but they will take up more floor space.
Conclusion
Air compressors are indispensable tools for achieving high-quality, efficient laser cutting. They assist in cooling the laser, preventing oxidation, clearing debris, and increasing cutting speed. By understanding the different types of compressors available and how to choose the right one for your needs, you can optimize the performance of your laser cutting machine and ensure a smoother, faster, and more precise cutting process.
When selecting an laser cutting machine compressor, keep in mind the required airflow, pressure, energy efficiency, and ease of maintenance. Investing in the right compressor not only improves the performance of your machine but also enhances the overall quality of your laser-cut products. With the right setup, your laser cutting operations can reach their full potential, increasing both productivity and profitability.